
Welcome!
Below are my projects organized by company!




Noise Barrier Assembly on Cyber Truck
Problem: User experience while on the main cabin was unacceptably loud for production vehicles
Background: When I started my internship at Tesla, the Cyber Truck was almost being released for customers. The scope of the project was supposed to be implemented later on, however, there was a change of priorities.
Challenges: The timeline from concept to physical parts on the vehicle was 5 weeks. Many changes in
scope and limited time.
Solution: A 4 decibel reduction in the main cabin in exchange of 2kg and $18

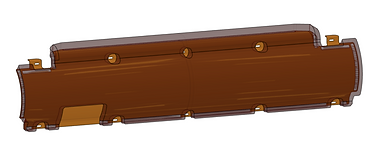
Low-Production
Responsible for material planning and sourcing within three weeks before launch! For context, prototype Injection molding parts take up to 8 weeks to manufacture.
​
Trained factory associates for assembly and integration. Created assembly documentation for factory associates as well as tier suppliers.
​

High Production
Met with stakeholders to determine all design requirements.
Owned the design, spoke with suppliers, negotiated prices, proactively identified methods to decrease landed costs.
​
Worked closely with other teams at Tesla for serviceability, validation, testing as well as integration.

Tow-Eye Cover Tether for Model X
Problem: Customers reported quality issue where Model X cars were delivered without tow-eye cover
Background: Tow-eye cover was being removed during end of line and not replaced. The tether was tested and trialed and was reported to not be strong enough
Challenges: 3D printed material is not representative of injection molded plastic.
Solution: Design reinforcement and tested

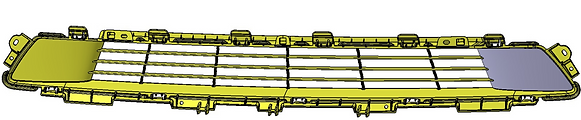

Iterated through multiple methods to reinforce the tether while keeping it light and making minimal changes to the current injection molded tool. Added ejection areas due to the size and thickness of the part. Increased snap retention and decreased deformation using beam analysis principles.

Rear fascia license plates
Problem: No brackets nor visible dimples on fascia while world-wide license plates are mounted
Background: New vehicle is under development. For this vehicle, we will not be providing any license plate brackets therefore it was my job to accomodate for countries around the world.
Challenges: Undefined licence plate dimensions and mounting requirements for European countries.
Solution: Engineered a commonized hole pattern on rear fascia that remains hidden with license plates mounted
Reached out to contacts world-wide
Compiling license plates dimensions and attachment customs/requirements
Categorized license plates based on size and attachment hole patterns
Met with other teams world-wide to establish a commonized data base
Engineered an attachment strategy that aligned with world-wide homologation

North America, AU Region, Europe, commonized attachment pattern is shown above respectively from top to bottom.
For China and Japan, there is a separate feature added to the fascia for fastening per country requirements and can not be molded.

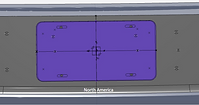


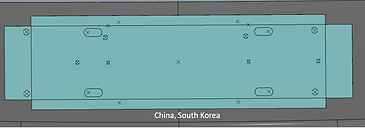

Autonomous Leak Fixture
Problem: Test over 1000 medical devices accurately for an ISO Standard for the FDA application
Background: When I started my internship at DEKA, the General Engineering Team (GET), was getting ready to formally test and validate the medical device. I was in charge of formulating not only the testing method but the fixture as well. Then, when we realized we needed to test over 1000 devices, my goal was to produce an autonomous remote controlled fixture
Challenges: The medical device is small and needed accuracy down to 0.020'' for accurate testing. Additionally, any testing should not hinder the performance of the device.
Solution: An automatic testing fixture that tests up to 5 medical devices simultaneously

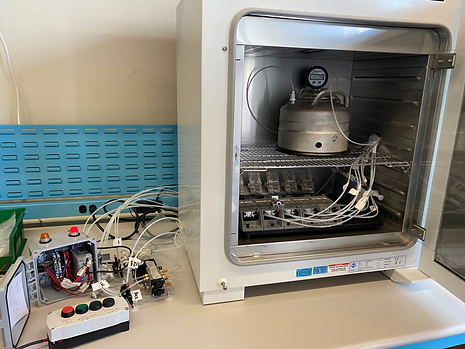
Finalized Fixture: Autonomous, 5 Medical Devices, 3 ISO Tests




For this project, I had ownership of the design. I prototyped myriad of mechanisms and gripper assemblies. I ran preliminary testing to determine the forces the fixture needed to exert. I wrote and tested my own code. I took initiative to learn about control systems and applied that knowledge to the final fixture. Initially, I made a fixture to test a single medical device as a proof of concept. However, as the scope of the project grew, I worked alongside another engineer at DEKA, Solomon Wells, to develop the scaled version of the fixture.
Initial Iterations: Single Medical Device Design

Hand Held Instron
Problem: The testing facilities were a bit of a trek from the G.E.T team and I needed to quickly test forces
Background: I needed to determine the force needed to occlude the medical device in order to have the proper gripper geometry and pneumatic services
Challenges: The mounting holes for the linear slide were off-center and asymmetrical, but it was fun to reverse CAD it.
Solution: A portable force gauge with a discrete linear slide
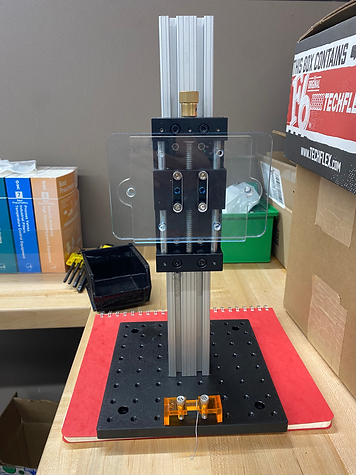

Safety Wall
Problem: STEM Center needed to showcase of its personal protection equipment
Background: When I took this personal project to enhance the STEM Center, I wanted it to be aesthetic. I worked with a partner. I took ownership of the safety glasses and headphone display.
Challenges: Goggles come in different shapes and sizes. How do I establish a method to hold them that is visually appealing?
Solution: Heat bend acrylic into a stand with 3D printed custom designed goggle holders.
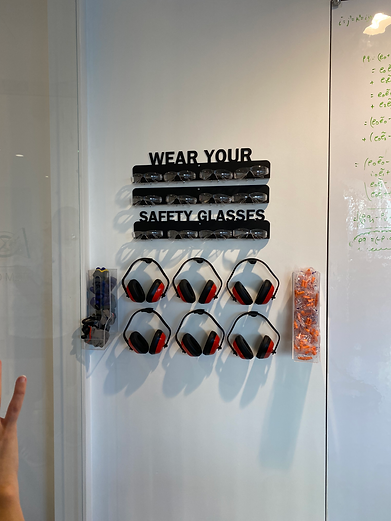
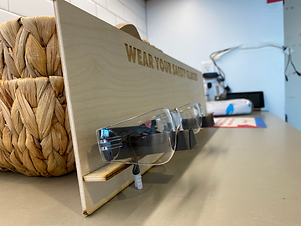




Beginner's Guide to Building an Intake Mechanism
Problem: One week to prep 6 kits of over 200 parts for a professional development with the resources at the STEM Center while simultaneously creating an intake mechanism for them with the parts in the kits
Background: The NYC FIRST STEM Center at Cornell Tech was training the first generation of teachers for the robotics based school Gotham Tech. Our goal was to introduce them to robotics and train them in the basis of FIRST and robotics. We also ran a summer program for the rising ninth graders attending Gotham Tech.
Challenges: We had one week to prepare content and materials.
Solution: A intensive guide on how to assemble an intake mechanism with a simple claw design

_HEIC.png)
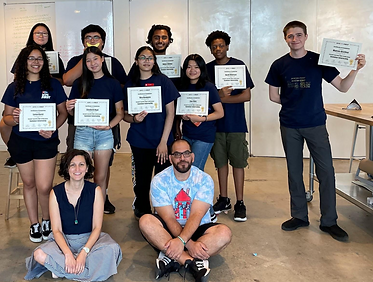